HUGG ser muligheter
Selskapet besitter et spennende mekanisk ingeniørteam som foruten rene mekaniske produkter har spesialisert seg på å pakke elektronikk for å tåle ekstreme miljøpåkjenninger. – Vi har mange eksempler på slike prosjekter, og jeg tror vi kan tilføre elektronikkindustrien mye på dette området, sier daglig leder Håkon Strømberg i Hugg AS.
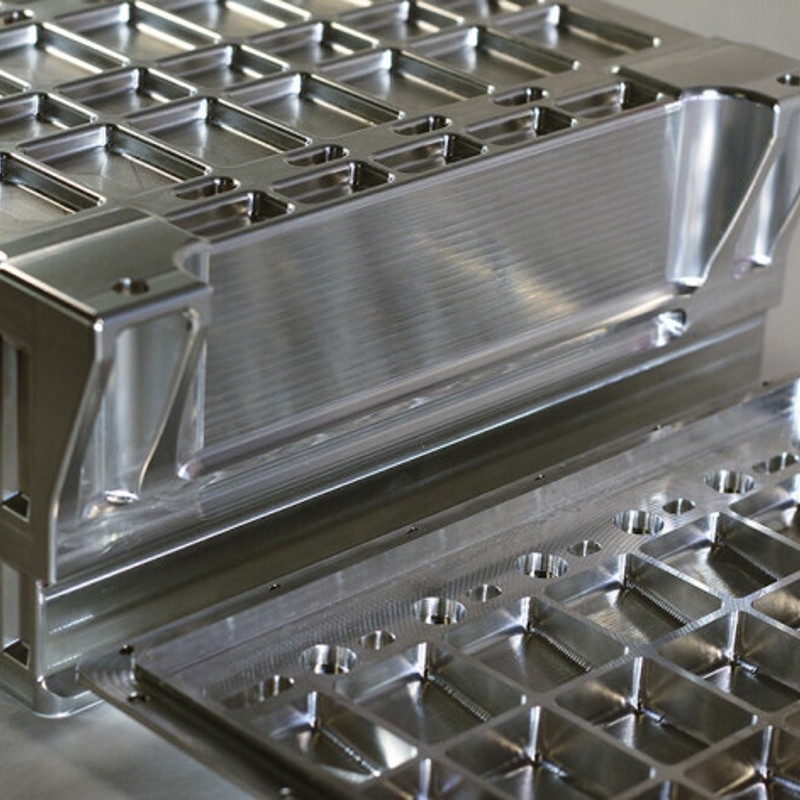
EAS fikk i oppdrag av European Space Agency (ESA) å designe og bygge batteripakken som skal sørge for elektrisitet til å utløse siste separasjonstrinn på ESAs nye Vega C Ariane-rakett. Hugg har designet, analysert og bygget prototypen som innkapsler batteripakken til EAS Batteries. Sentralt var også bruk av en rekke dataverktøy, inkludert responsspekter- og vibrasjonsanalyser.
Batteripakke til rakett
De har blant annet utviklet en batteriinnkapsling for bruk ombord i bæreraketten Vega C. Den skal sørge for å holde på plass en batteripakke som skal brukes til å løse ut det siste trinnet i raketten, og må tåle krefter på inntil 10.000 g. Kapslingen, som er maskinert i aluminium, er tatt frem ved bruk av kompetansen på huset, kombinert med avanserte dataverktøy, og har gjennomgått omfattende testing.
Finn sauen
I den andre enden av skalaen finner vi et langt mer jordnært produkt, bokstavelig talt, den elektroniske sauebjellen FindMy, som inneholder gps- og kommunikasjonselektronikk for å holde rede på hvor sauene er. Å dingle rundt under en sau i all slags terreng og vær er ingen spøk, og elektronikken, som ved hjelp av batteri skal holde det gående i et helt år mellom hver lading, er innstøpt («pottet») i kapslingen.

Hugg har designet den mekaniske løsningen som innkapsler elektronikken i den elektroniske sauebjellen FindMy. Under designprosessen var det viktig at designet ble sterkt slik at den håndterte de ytre påkjenningene slike bjeller utsettes for. Designet ble optimalisert for plaststøping og masseproduksjon for å minimere enhetskostnaden.
Offshoreteknologi
Begge disse anvendelsene omfatter påkjenninger og krav som minner om det ting utsettes for i olje- og gassbransjen, og det er nettopp herfra Hugg henter mye av sin erfaring. Strømberg selv startet i sin tid det offshore-rettede utviklingsfirmaet Nemo Engineering, som raskt vokste til 180 ansatte. Selskapet ble solgt til Kongsberg Gruppen i 2012, og noen år etter (i 2015) hoppet Strømberg av og startet Hugg AS sammen med Ulf Lønnemo.
Militær mekanikk
Bakgrunnen for oppstarten var blant annet kontakten med Galleon Embedded Computer AS (Elektronikk nr. 12 – 2018), en avlegger av kortmodulleverandøren VMETRO (solgt til utlandet i 2008 og senere lagt ned). De hadde behov for ekstremt robuste mekaniske løsninger til sine lagringsmoduler til forsvar og luftfart, og etter at Strømberg og Lønnemo utviklet det første designet, har Hugg levert alt av mekanikk til Galleon.
Tung kompetanse
– Vi kan løse mye i Norge, understreker Strømberg. – Ikke minst basert på erfaringen fra Nordsjøen; For vår del betyr det at vi har tung kompetanse på analyser, materialvalg, korrosjon, vibrasjon/miljø og meget annet. Ikke minst dokumentasjon, fremholder han. – Slik sett er det ikke så stor overgang fra f.eks. offshore til forsvar eller romfart, poengterer han.
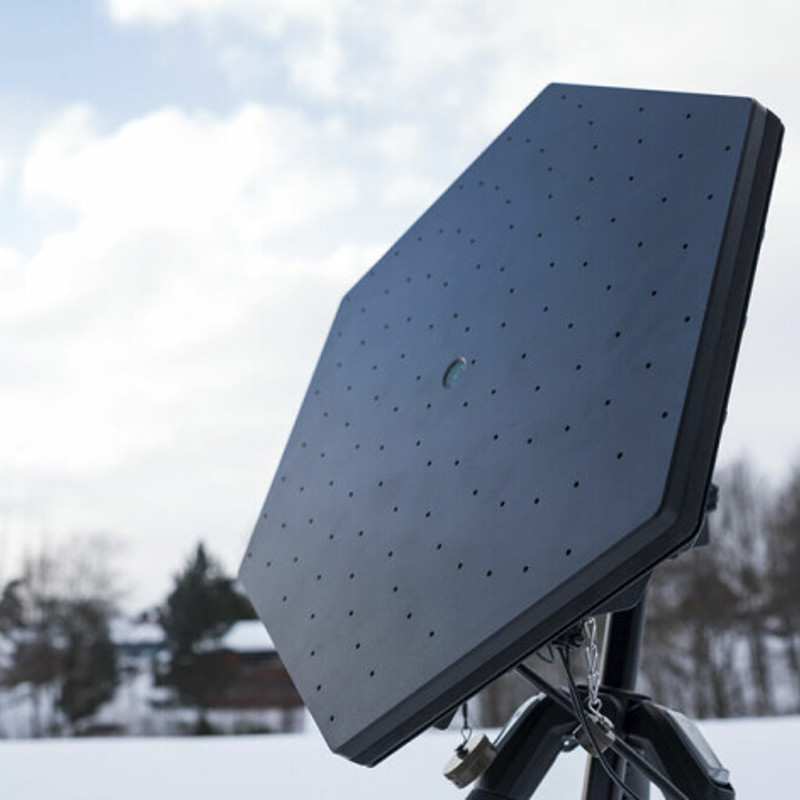
Selskapet har vært en partner for Squarehead siden 2014 og har siden da levert brorparten av mekanisk utstyr som de benytter i sine akustiske kameraer.
Muligheter i elektronikk
Hugg har nå vokst til å omfatte et kompetent ingeniørmiljø med 9 ansatte i Oslo, samt en utviklingsavdeling i Krakow, Polen med 3 ansatte. Strømberg ser mange muligheter innenfor mange segmenter av elektronikkindustrien. – I disse koronatider har vi blant annet vært med å utvikle innpakning til en elektronikkenhet som skal styre respiratorer.
Respirator
– Løsningen skal samkjøre respiratorens bevegelser med pasientens egen pust, og må tilfredsstille strenge krav til EMC og sikkerhet, i henhold til standarder for medisinsk teknisk utstyr, påpeker han. De første 15 enhetene er i skrivende stund allerede ute, og flere er på vei. Løsningen ble utviklet på bare 3 måneder, noe Strømberg betegner som «ganske kjapt».
Kule utviklere
– Et viktig poeng er at det er mange kule utviklere der ute som vi samarbeider med, og som tenker nytt. Et godt eksempel på det er sauebjellen FindMy, som allerede har rukket å bli en kjempesuksess. Den første serien på 5000 som Axxe produserte, ble nærmest revet vekk, og de må øke produksjonen, forteller Strømberg, som også utpeker landbruk som et viktig marked fremover på generell basis.
HUGG, OMNIs spesialist innenfor mekanikk, les mer om OMNI spesialistene: Spesialistene