Tverrfaglig samarbeid ga det optimale subsea-batteriet
Oppdraget
OMNIs batterispesialist SCHIVE AS designer, tester og produserer skreddersydde batteriløsninger som skal «powre» applikasjoner som opererer i ulike og krevende miljøer med høye krav til driftssikkerhet og kvalitet. De hjelper kunder innenfor segmenter som subsea, offshore, forsvar, industri, IoT med flere.
Som et av landets fremste kompetansesentre på batterier ble SCHIVE for en tid tilbake kontaktet av en kunde med behov for stabil og sikker strømforsyning til en subsea sensor-applikasjon som skulle installeres på 200 meters dyp i Nordsjøen. Kunden var avhengig av et subsea-batteri som kunne være operativt døgnet rundt, syv dager i uken og over en periode fra høst til vår. Videre presenterte kunden følgende hovedutfordringer:
1. Det vil ikke være tilgang til batteriet i bruksperioden og det må kunne operere 8 måneder i strekk på havbunnen, uten mulighet for vedlikehold.
2. Batteriet skal hentes opp av vannet på våren, demonteres og vedlikeholdes på en praktisk måte. Dette innebærer at battericellene skal skiftes ut og at subsea-batteriet skal klargjøres for utsetting påfølgende høst for nye 8 måneders drift på havbunnen.
I samråd med kunden ble man enige om at mekanikken og batteripakken i sin helhet skulle dimensjoneres for maksimal sikkerhet og der hensynet til bærekraft også måtte ivaretas. Behovet for utbytting og kast av deler skulle være minimalt og flest mulig komponenter skulle kunne gjenbrukes gjennom batteriets totale levetid, som forventes å være mellom fem og ti år.
OMNI-nettverkets aktiveres
Kundens ønske om høy grad av gjenbruk kombinert med maksimalt sikkerhetsnivå stilte store krav til robusthet og nøyaktighet for alle komponentene som skulle integreres i batteripakken, alt fra elektroniske koblinger og styringsmekanismer til den mekaniske løsningen og batteriets innkapsling.
For å være i stand til å levere et komplett subsea-batteri klar for bruk og med disse spesifikasjonene, var vi avhengige av tverrfaglig samarbeid og tilførsel av komplementær kunnskap på tilstøtende fagfelt, sier Erik Hagelien fra SCHIVE AS. Som medlem av spesialistnettverket OMNI hadde vi tilgang til all den nødvendige kompetansen gjennom de andre bedriftene i nettverket. Tanken med OMNI er jo at flere spesialister som jobber systematisk sammen, gir bedre produkter, fortsetter han. Innad i OMNI er vi vant til å samarbeide i et bredt spekter av prosjekter. Dette nyter kunden godt av fordi samhandlingen og prosessene blir mye enklere, samt at vi unngår design - og produksjonsblemmer underveis.
I SCHIVE gjorde vi kapasitetsberegninger for valg av rett batterikjemi og for å dimensjonere batteriet for garantert oppetid i 8 måneder, der temperatur og andre variabler ble tatt i betraktning. Kjemivalget ble Lithium Thionyl Chloride (SOCl2), bobbin primærceller (engangsbatterier).
OMNIs spesialist på design og simulering av mekaniske løsninger, Hugg AS, bidro med design og anskaffelse av subsea-kannen som battericellene skulle monteres i. Dette innebar beregninger og tilpasninger for å gjøre kannen i stand til å motstå det trykket den blir utsatt for utenifra, og ikke minst en overtrykksventil som skal forhindre en potensiell eksplosjon ved komplikasjoner inne i kannen. En annen mekanisk utfordring var at subsea-kannen måtte ha et lokk for å kunne åpnes når battericellene skulle byttes etter de 8 første månedene på havbunnen. Det var essensielt at denne løsningen måtte være hundre prosent tett.
Videre måtte vi sammen finne smarte løsninger for sammenkopling av battericellene til staver i en 7S konfigurasjon for riktig spenning samtidig som opptil 90 staver skulle koples sammen i parallell for å oppnå ønsket kapasitet. Dette ble en mekanisk utfordring da batteri stavene må stå helt støtt og ubevegelig inne i subsea-kannen. SCHIVE med sin batterikompetanse beregnet også inn en sikkerhetsavstand mellom alle batteristabene som måtte ivaretas for å unngå varmeakkumulering og mulige uønskede situasjoner. Løsningen ble å designe et “plastskjelett” (POM) som skulle holde batteri stavene på plass inne i kannen og garantere sikkerhetsavstanden mellom dem. Her var OMNIs plastspesialist Miko Plast AS en viktig bidragsyter.
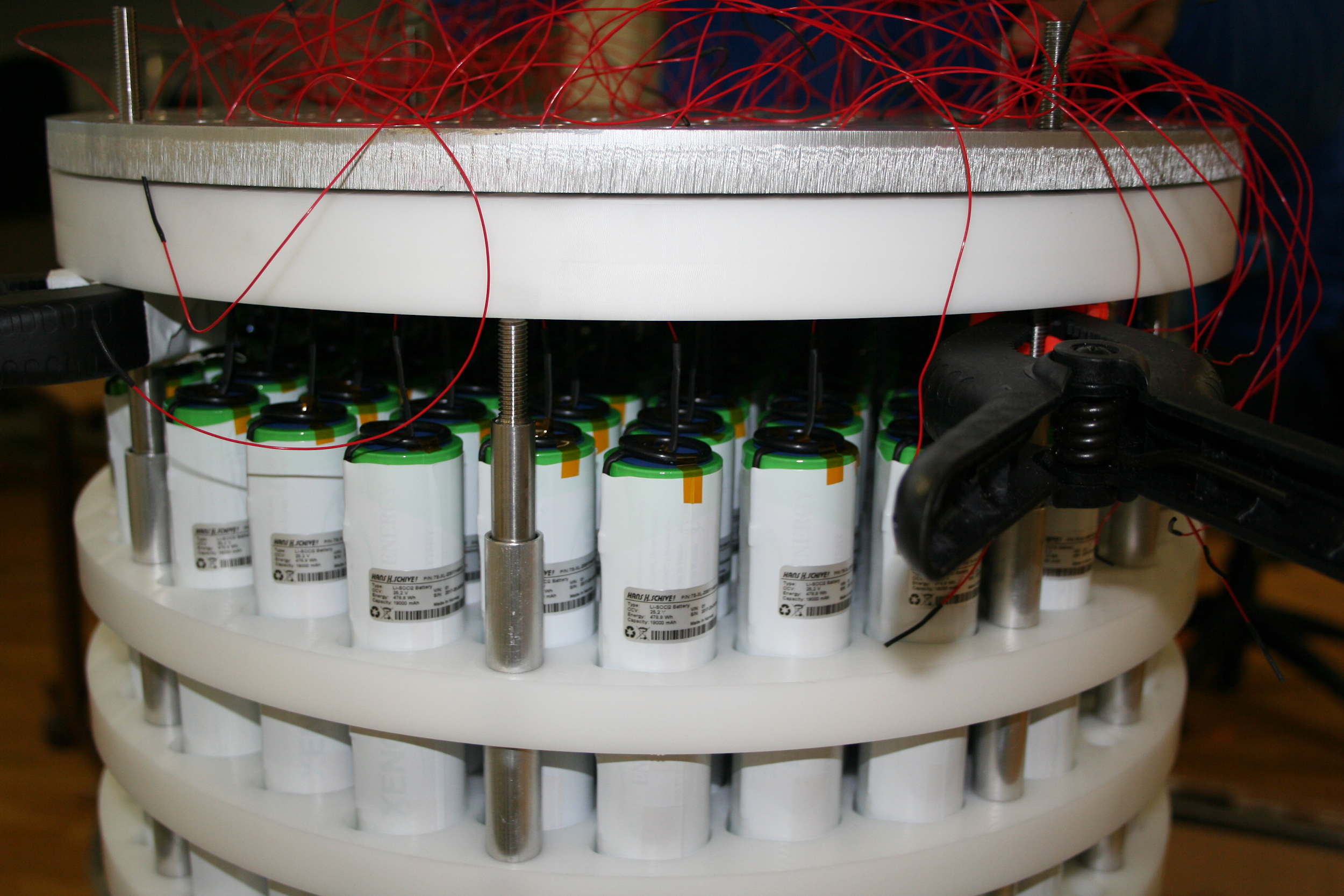
Miko har inngående ekspertise på løsningsdesign, valg av riktig plastmateriale og plastproduksjon. De fikk produsert plastskjelettet ved deres egen fabrikk i Ytre Enebakk utenfor Oslo før det i sammenstillingen av batteripakken ble boltet sammen ved hjelp av stenger i syrefast stål.
For å ivareta viktige sikkerhetsfunksjoner i subsea-batteriet, utviklet OMNIs spesialist innen elektronikkutvikling, 7Sense Technologies AS, beskyttelseselektronikk i samråd med de andre spesialistene.
Denne elektronikken ble så produsert og testet i henhold til IPC-A-610-Kl. 3 av OMNIs elektronikkprodusent AXXE AS som har sin fabrikk i Halden, Østfold. Ristetest av elektronikken inngikk i kravspesifikasjonen.
Til slutt ble subsea-batteriet sammenstilt og klargjort for levering og bruk ved SCHIVEs produksjonslinje i Asker utenfor Oslo.
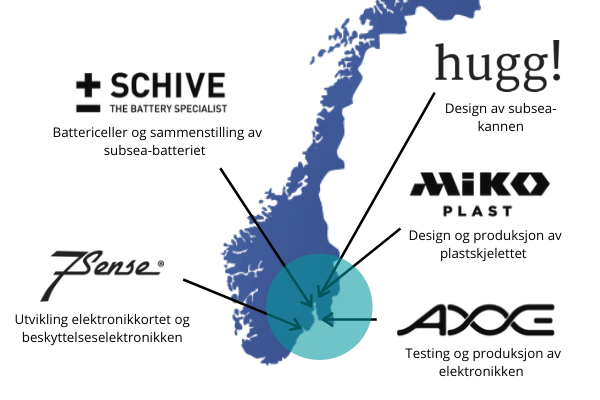
Resultatet
Subsea-batteriet ble levert etter planen og har nå operert i Nordsjøen i rundt tre år. Etter hver sesong har det blitt heist opp for bytte av primærceller, mens det meste av mekanikken og elektronikken har blitt gjenbrukt over disse årene.
Tanken om gjenbruk av komponenter ga kunden en høyere inngangskostnad, men byr på betydelige kostnadsbesparelser etter hvert som batteriet har hatt flere sesonger i drift på havbunnen, sier Steinar Lein fra Miko Plast AS. Da vi utviklet produktet i OMNI hadde vi ingen marginer for feil i design eller produksjon og vi måtte være svært nøyaktige for at de ulike komponentene skulle passe sammen og tåle bruken de skulle bli utsatt for. I praksis betyr det at utviklingen av alle løsningene til subsea-batteriet skjedde parallelt og at alle spesialistbedriftene ble involvert i samtlige prosesser. Her er nærhet et viktig stikkord, fortsetter han.
- I OMNI kjenner vi hverandre, vi har tett kontakt gjennom hele prosessen og kan på kort varsel møtes ansikt til ansikt for å løse tekniske utfordringer. Ikke minst så har kunden kun én partner å forholde seg til, noe som forenkler logistikken betraktelig. Dersom man går til ulike leverandører på tvers av landegrenser blir avstanden fort for stor og det kan oppstå misforståelser og feil som medfører at man må ta et skritt tilbake og gjøre ting om igjen.
Håkon Strømberg fra Hugg AS legger til at de i OMNI er opptatt av at alle spesialistene blir involvert helt i begynnelsen av et prosjekt. - De ulike spesialistbedriftene sitter på unike erfaringer og når alle bidrar med sin spisskompetanse helt fra start, har vi muligheten til å ta alle produktets aspekter i betraktning før vi hogger ting i stein. Ofte avdekker vi forbedringspotensialer ved produktets funksjonalitet eller produksjonsprosess som kunden aldri hadde i tankene. Denne filosofien gir oss forutsetningen for å designe bedre produkter, tilpasse den mest effektive produksjonen og minimere risikoen for at vi gjør feil som må rettes opp senere i prosessen. Et konkret eksempel fra subsea-batteriet vi utviklet er at vi allerede i startfasen tok stilling til hvordan det skal heises ned og løftes opp fra havbunnen. Selv om det ikke angår batteriets primærfunksjon, påvirker dette aspektet andre deler av produktet og dets produksjon. Vi kunne fort endt opp med å måtte gjøre endringer senere i prosessen dersom vi hadde glemt å se produktet på en helhetlig måte helt fra start.
For mer om OMNI medlemmer og Schive se Spesialistene